How Can We Help
+48 519 821 507
contact@hosseg.com
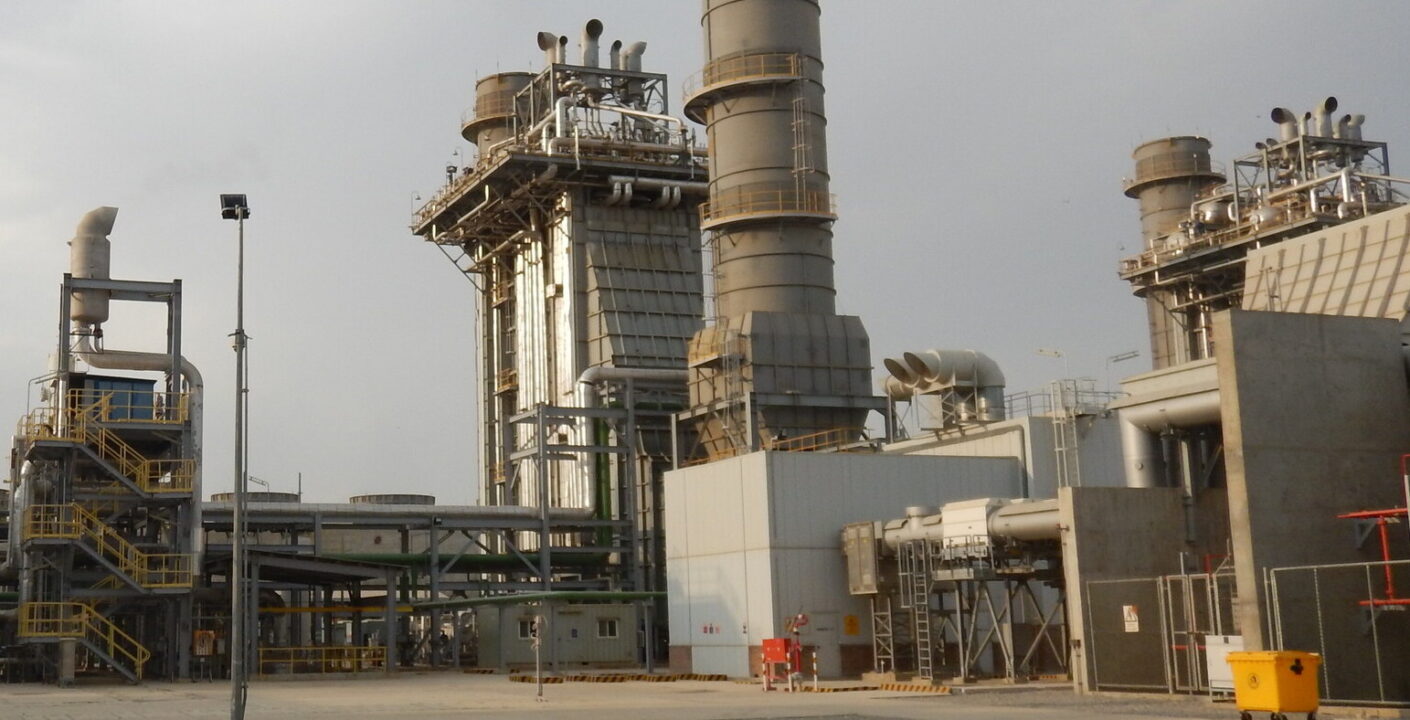
Process Efficiency Optimization
At Hosseg, we focus on enhancing industrial process efficiency, offering advanced solutions for software adjustments and hardware modernization. With years of specialist experience, we effectively analyze and improve control and monitoring systems, identifying key areas for enhancement.
Over time, industrial installations such as steam boilers, HRSG systems, flue gas and industrial gas treatment installations, and other process systems undergo natural wear. As a result, control and monitoring precision gradually declines, leading to reduced operational efficiency. Equipment operating parameters change, and software originally tailored to operational conditions becomes outdated. In such cases, system recalibration or modernization of key components becomes necessary—often much faster than commissioning a new installation.
We specialize in the following areas:
- HRSG and Steam Boilers – optimizing heat recovery and steam production systems.
- Flue Gas Treatment Installations – improving treatment process efficiency.
- Process Equipment and Installations – enhancing reliability and performance.
- Pipelines – modernizing and adapting to new operating conditions.
- Flow Control – precise media flow management.
- Bulk Material Handling – streamlining transport and storage processes.
Our service is based on a comprehensive approach: we conduct detailed analyses, tests, and calculations to determine which elements—software or hardware—require optimization. We offer updates and enhancements to control and measurement systems, as well as replacement, modernization, or adjustment of installation components. This increases the efficiency, performance, and reliability of industrial systems, reducing failure risks and ensuring stable operation.
Hosseg is a partner that not only restores full installation functionality but also adapts it to current requirements, extending its lifespan and maximizing operational potential. Our expertise and specialization enable us to deliver tailored solutions, supporting clients in maintaining a competitive edge in demanding industrial environments.
CFD Analysis of Flue Gas Ducting
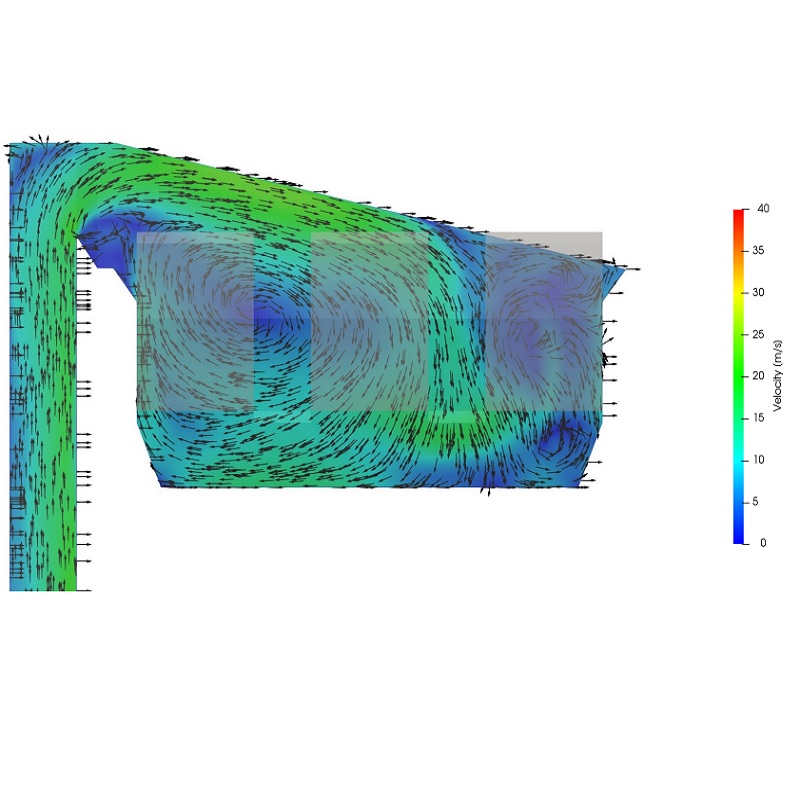
Determination of pressure drop in the flue gas duct
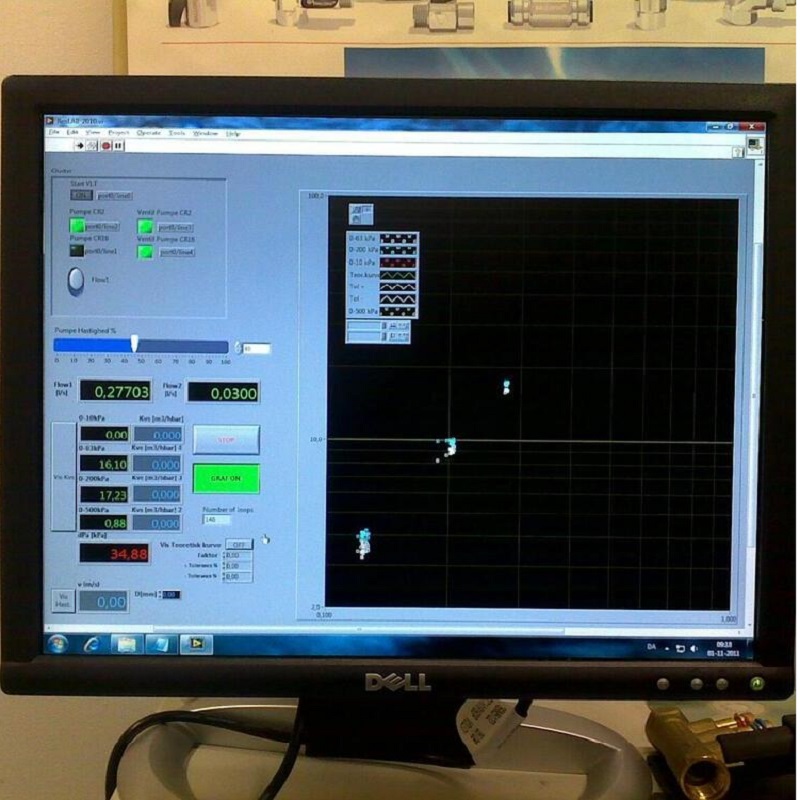
CFD simulation of air injection
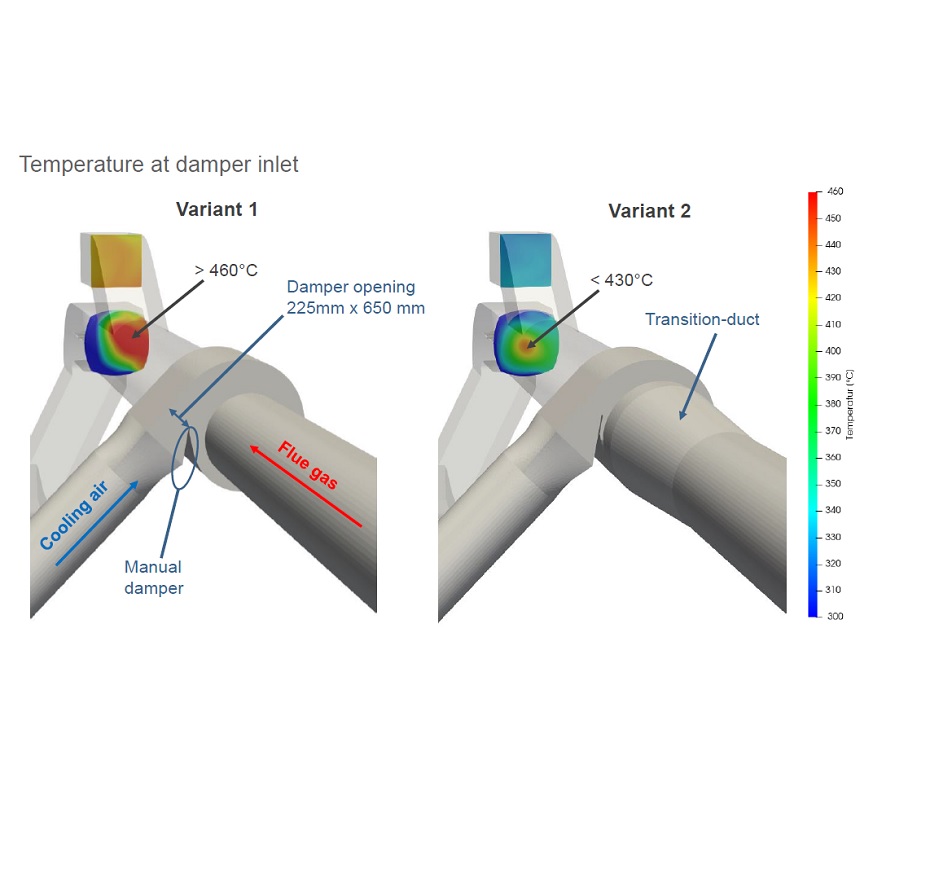
Determination of the Kv coefficient of the orifice
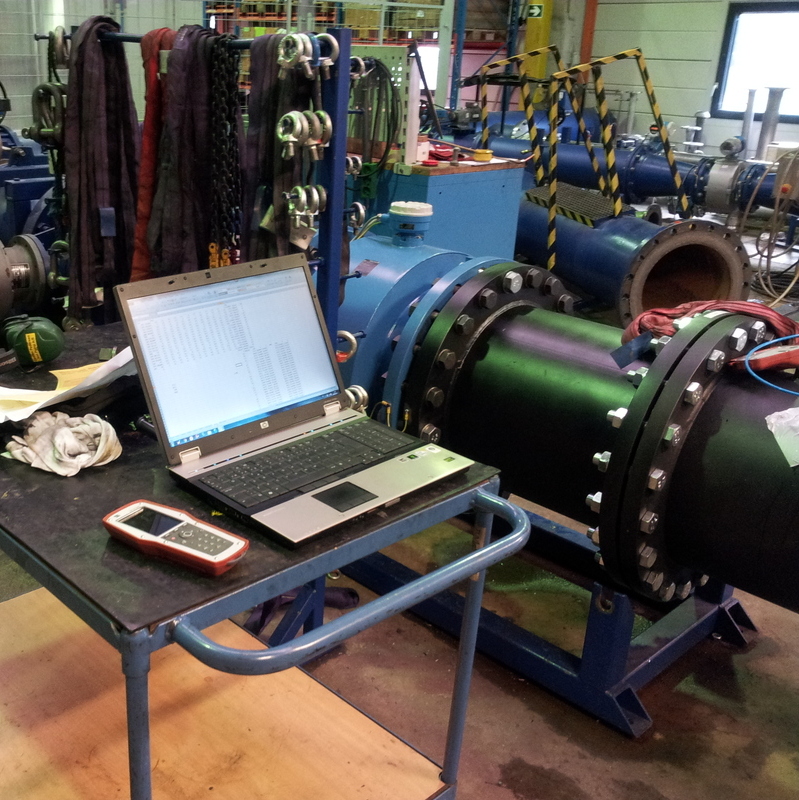