How Can We Help
+48 519 821 507
contact@hosseg.com
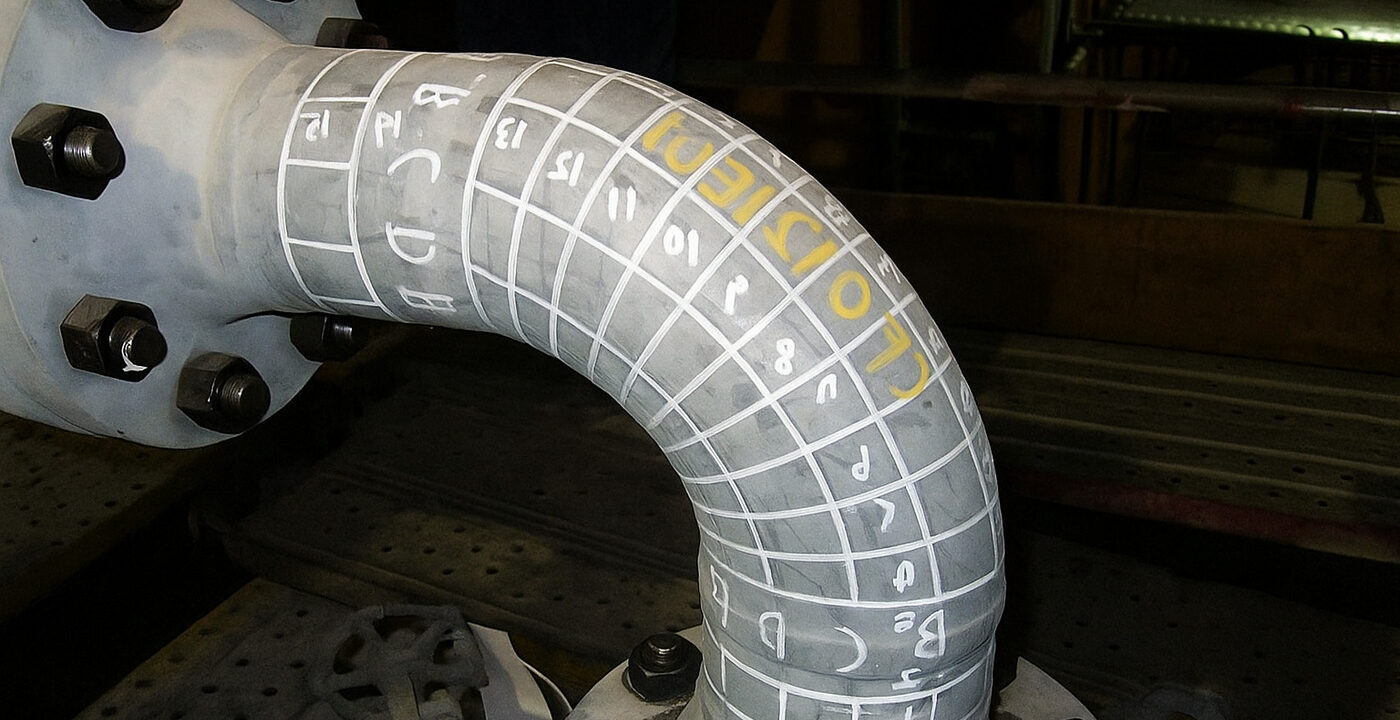
Comprehensive Testing and Measurement Services for Facilities
Hosseg delivers advanced facility testing and measurement supervision and execution services, critical for ensuring the reliability and safety of industrial installations. Our efforts focus on precisely assessing the technical condition of process equipment, energy machines, pipelines, and installations in facilities like conventional power plants, waste incineration plants, and complexes with flue gas treatment systems (e.g., desulfurization and dedusting installations).
We specialize in comprehensive diagnostics, using a risk-based inspection (RBI) approach to identify critical areas, minimizing failure risks, optimizing maintenance costs, and reducing downtime. Our offerings include:
- Visual inspections, including drone-assisted—surface and hard-to-reach area checks.
- Ultrasonic testing (UT)—detecting internal defects and material wear.
- Thermographic testing—identifying thermal anomalies and insulation leaks.
- Borescopic inspection—examining component interiors without disassembly.
- Flow measurements—analyzing media dynamics and optimizing transmission systems.
- Energy equipment diagnostics—assessing the technical condition of energy machines.
- Pressure installation diagnostics.
Pressure Installation Diagnostics
Pressure installations, compliant with international standards, require regular inspections to prevent failures. Degradation processes like fatigue cracks, material creep, corrosion-mechanical damage, or flow-assisted corrosion (FAC) are often invisible to the naked eye. Hosseg employs modern NDT techniques for early defect detection and full control over the technical condition of these components.
Our experts provide end-to-end management of testing and measurements, from operational data analysis and inspection strategy development to execution and result interpretation. We deliver detailed reports with recommendations for operation, maintenance, or modernization, ensuring compliance with ASME, API, and EN standards.
Combining innovative technologies with specialist expertise, we offer both supervision and independent testing execution. Our services enhance infrastructure reliability, extend installation lifespan, and reduce operating costs. Hosseg is a strategic partner supporting the stability and growth of industrial facilities at the highest level.
Advanced Facility Diagnostics
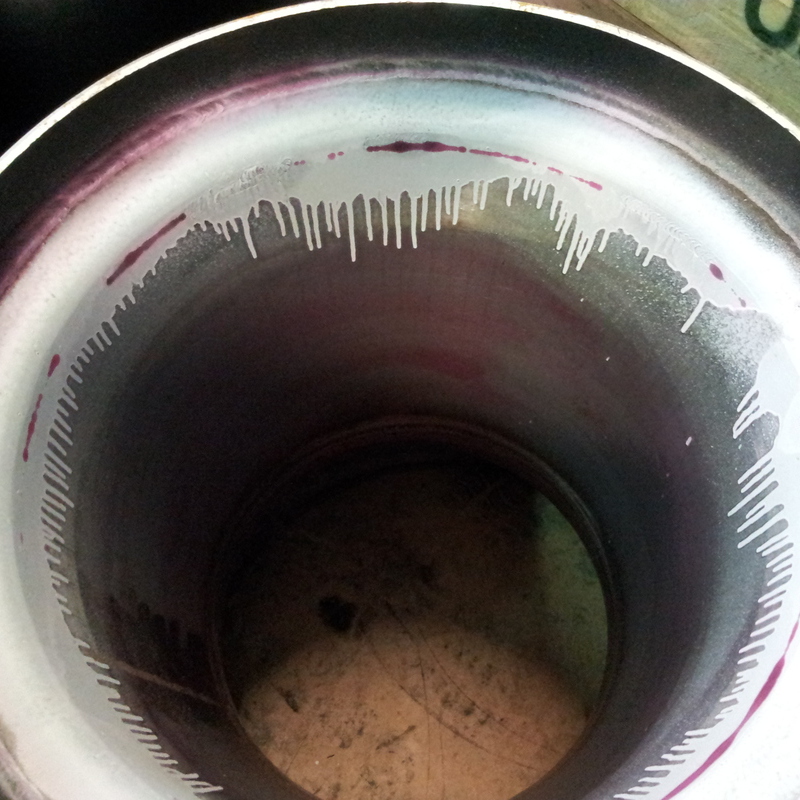
02.
Use of Modern Testing Methods
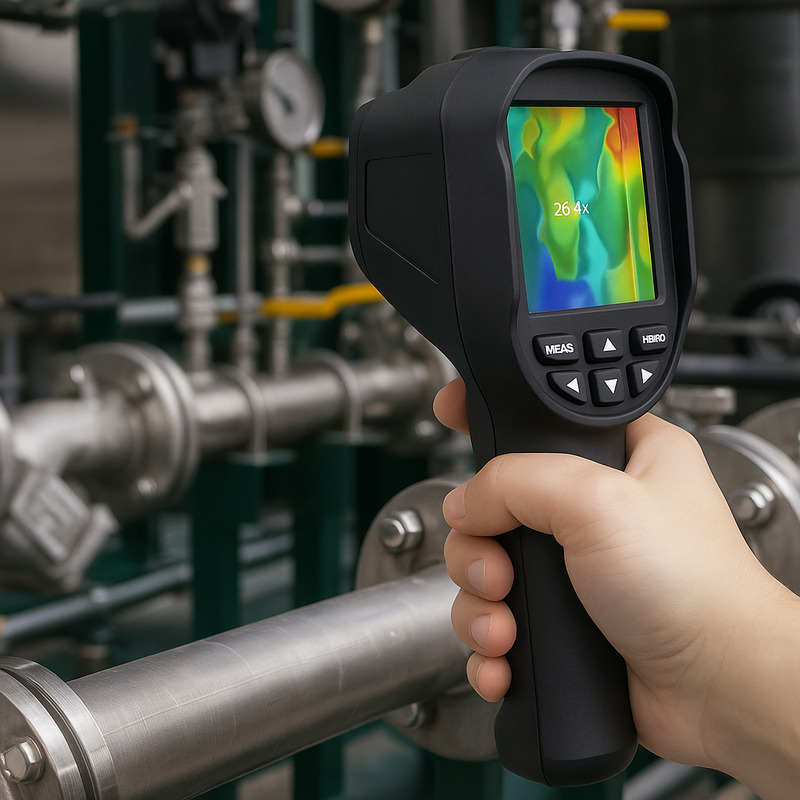
Specialized Pressure Installation Oversight
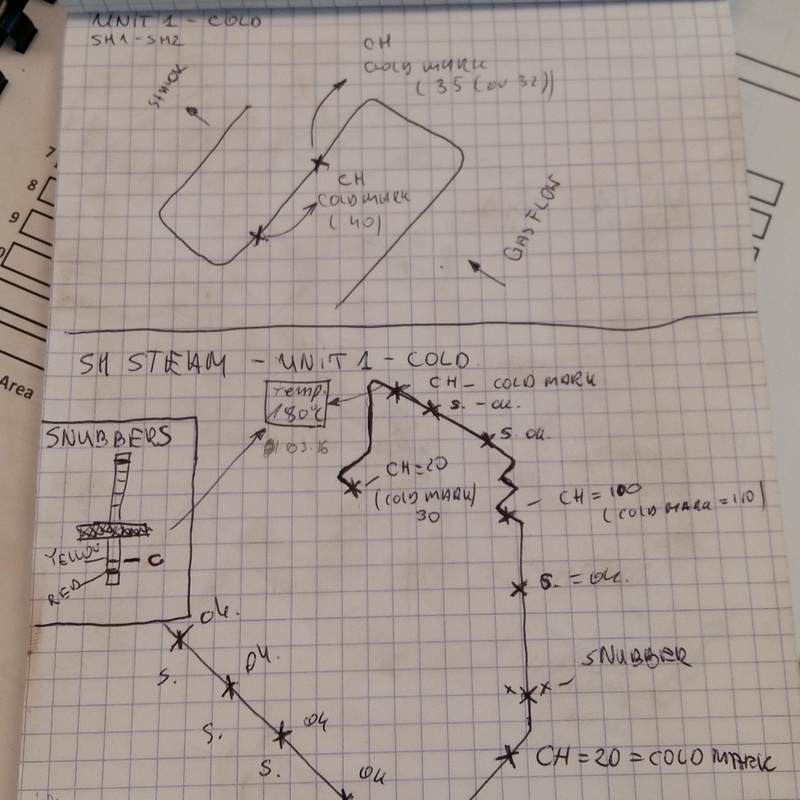
Full Testing Management and Operational Recommendations
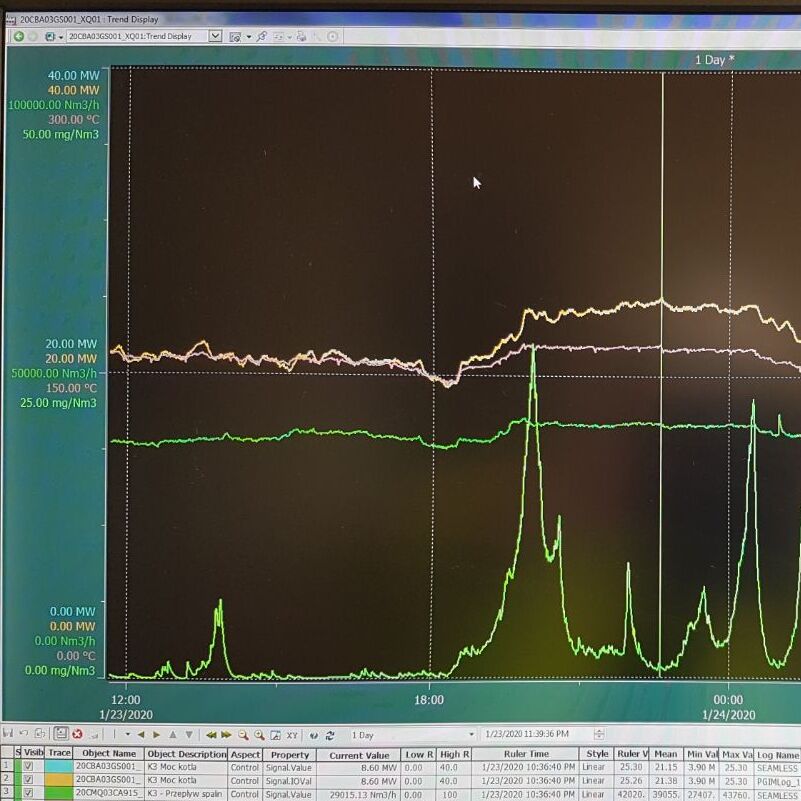